Waste2Fuels
Waste2Fuels - Sustainable production of next generation biofuels from waste streams
Duration: 2016 – 2018
Background
Renewable energy carriers and biofuels are of increasing interest on our way to a sustainable energy economy. One of the most promising biofuels from a technical perspective is bio-butanol. It offers high energy density combined with low volatility and corrosiveness compared to other liquid biofuels like bio-ethanol.
Waste2Fuels aims to produce biobutanol from agrofood waste (AFW) streams as a sustainable alternative for use as a direct substitution for virgin fossil fuels.
Traditional production route of bio-butanol uses bacteria (e.g. Clostridium acetobutylicum) to transform biomass to acetone, butanol and ethanol. This mixture is then separated by distillation obtaining pure bio-butanol. The main problems of this route are the self-inhibition of the used bacteria at butanol concentration above 1.5 wt% and the high energy demand of the distillation due to the low butanol concentration. Therefore, one of the main challenges towards an economically feasible bio-butanol is to increase bio-butanol productivity and concentration as well as avoiding self-inhibition. Possible options to achieve this are innovative bioreactor concepts, in-situ removal of bio butanol and the use of modified bacteria.
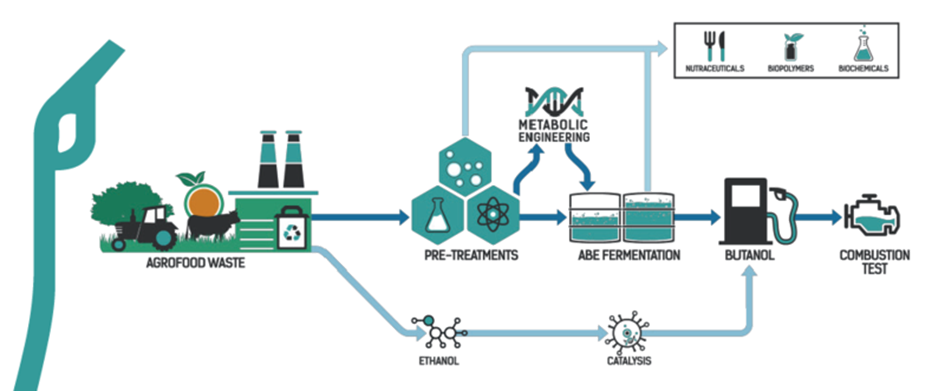
Figure 1: Research activities in Waste2Fuels
Project consortium and role of ICEBE
A consortium consisting of 20 partners from academia as well as industry ensures both high quality research and focus on fast commercialization making this project a great chance towards a sustainable and renewable energy economy.
The Institute of Chemical, Environmental and Biosience Engineering (ICEBE) is responsible for the development and evaluation of pervaporation techniques for in-situ butanol removal as well as the simulation and assessment of the overall process.
A detailed overview about the consortium and the role of each project partner can be found at the official Waste2Fuels homepage.
Methods
Multiple membrane modules are tested for their applicability in an in-house developed test rig. Both commercially available materials, like Polydimetyhlsiloxane (PDMS), as well as new alternatives like Polyoctylmethylsiloxane (POMS) are considered. A general flowsheet and exemplary results can be found below.
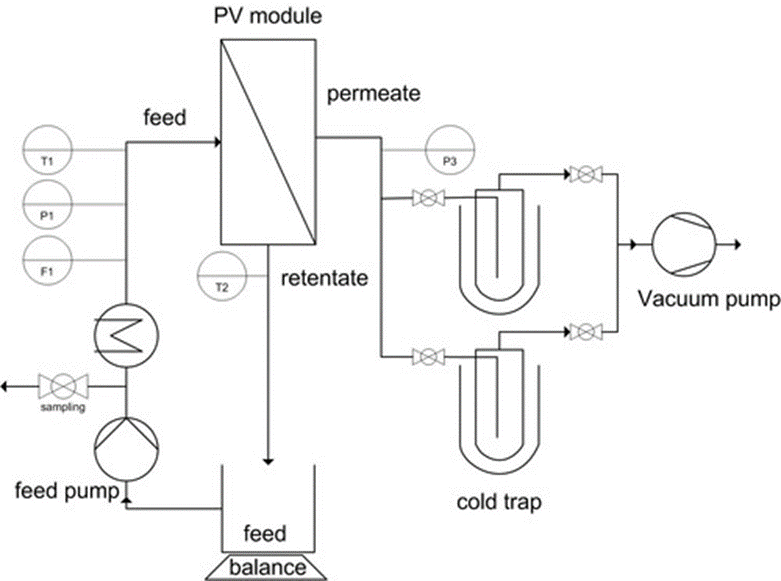
Figure 2: Flowsheet of the pervaporation unit
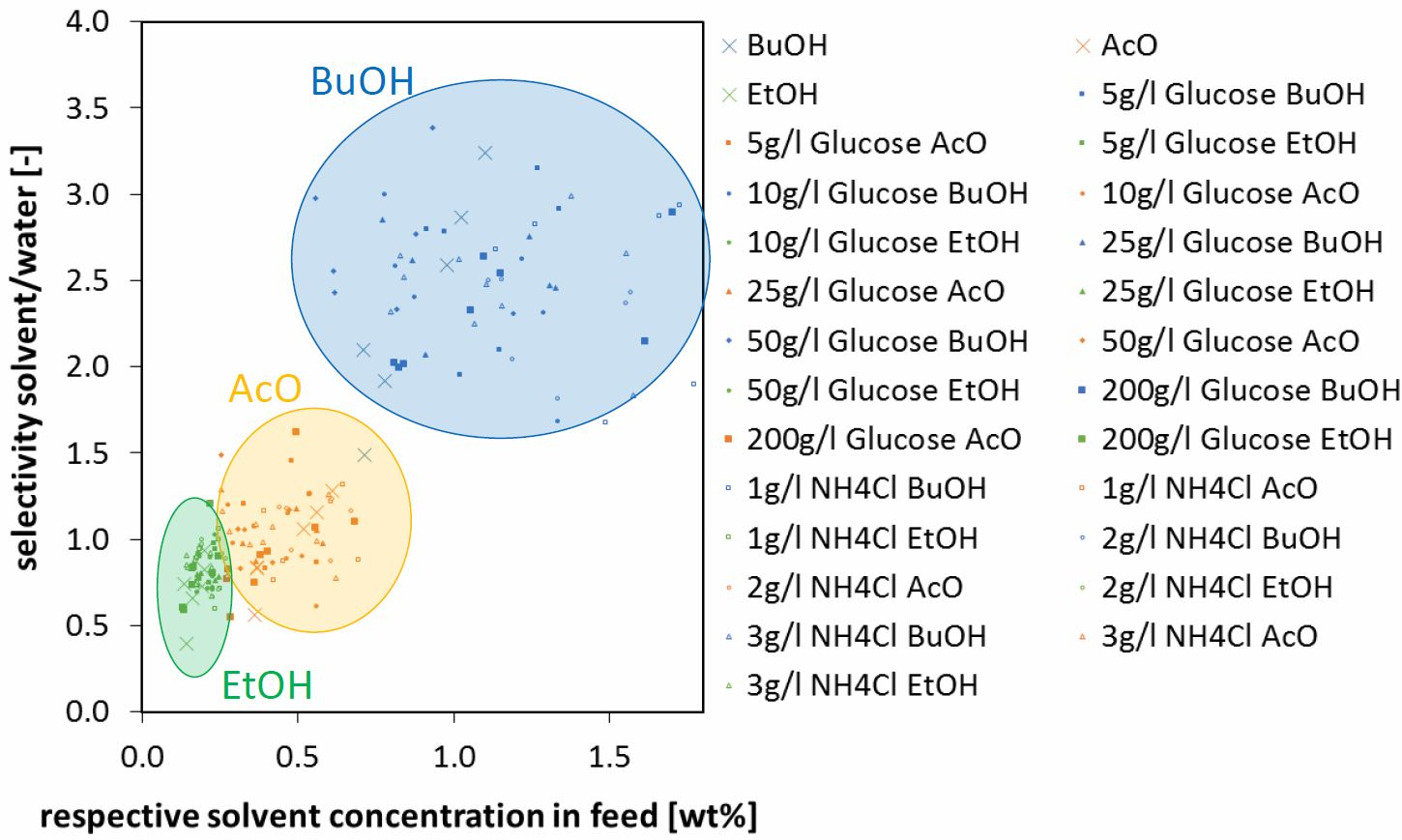
Figure 3: Exemplary results for selectivity of solvent/water
Experimental data and results generated by project partners focusing on other upgrading technologies like adsorption and gas stripping are used to set up a simulation model of the overall process using the process simulation software Aspen Plus®. This offers the possibility to assess mass and energy balances of an up-scaled process and chose the preferable overall process design.
Funding
This project has received funding from the European Union’s Horizon 2020 research and innovation program under grant agreement No 654623”.

Go to top